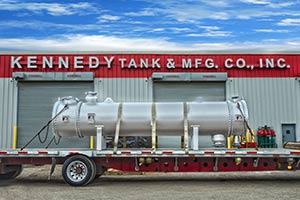
DynaChem
For heating and cooling liquids and gasses to precise temperatures in specific time frames, shell and tube heat exchangers are a very common and logical process solution. Kennedy Tank is a proud member of both the American Society of Mechanical Engineers (ASME) and the Tubular Equipment Manufacturers Association (TEMA). We manufacture our shell and tube heat exchangers to meet the rigorous standards of these two recognized organizations. We comply with all industry standards and practices as well as the common design criteria of specific industries.
Kennedy has manufactured shell and tube heat exchangers for a wide range of applications. Our heat exchangers are used in a variety of industries including petroleum, utility, paper, chemical, rendering and metals. Applications are as diverse and demanding as the oil fields of Alaska, off-shore platforms from the Gulf of Mexico to the South China Sea, refineries in Canada and fermentation plants in Mexico. Kennedy heat exchangers are operating in applications as exotic as dual condenser / reboilers for uranium fuel enrichment processes and as common as product coolers and glycol to glycol exchangers.
When it comes to shell and tube heat exchangers, Kennedy Tank has earned a reputation for quality, dependability and value. Our heat exchangers are designed to satisfy the rigid requirements of the toughest industries, including:
- Pharmaceutical
- Chemical
- Petroleum
- Petrochemical
- Steel / Metals
- Food & Beverage
- Rendering
- Power / Utilities
- Renewable Energies
Kennedy shell and tube heat exchangers are designed and fabricated to ASME code, TEMA standards, API-650 code, and to your own individual specifications. Custom designs are available from 2,000 psig to full vacuum, 1,200 degrees to -325 degrees Fahrenheit in carbon steel and virtually every alloy. Contact us to discuss your shell and tube heat exchanger needs.
Heat Exchanger Applications
Condensers
Evaporators
Glycol to Glycol exchangers
Heaters
Interchangers
Product coolers
Reactors
Heat Exchanger Services
Sandblasting
Painting
Passivation
Post-Weld Heat Treatment
Radiography
Helium Testing
Heat Exchanger Compliances
API 660
ASME code
TEMA standards
Heat Exchanger Quality Assurance
Leak Testing
Pressure Testing
QC Stamps on all welded / processed material
Liquid Penetrant Testing
Magnetic Particle Testing
Certified Welding Inspection
Certified Radiographic Interpretation
NACE Coating Inspection
Multiple Integrity Tests Performed On All Exchangers
Manufacturer of High Performance Alloys – Kokomo, Indiana